Streamlining the Milk Hauling Process
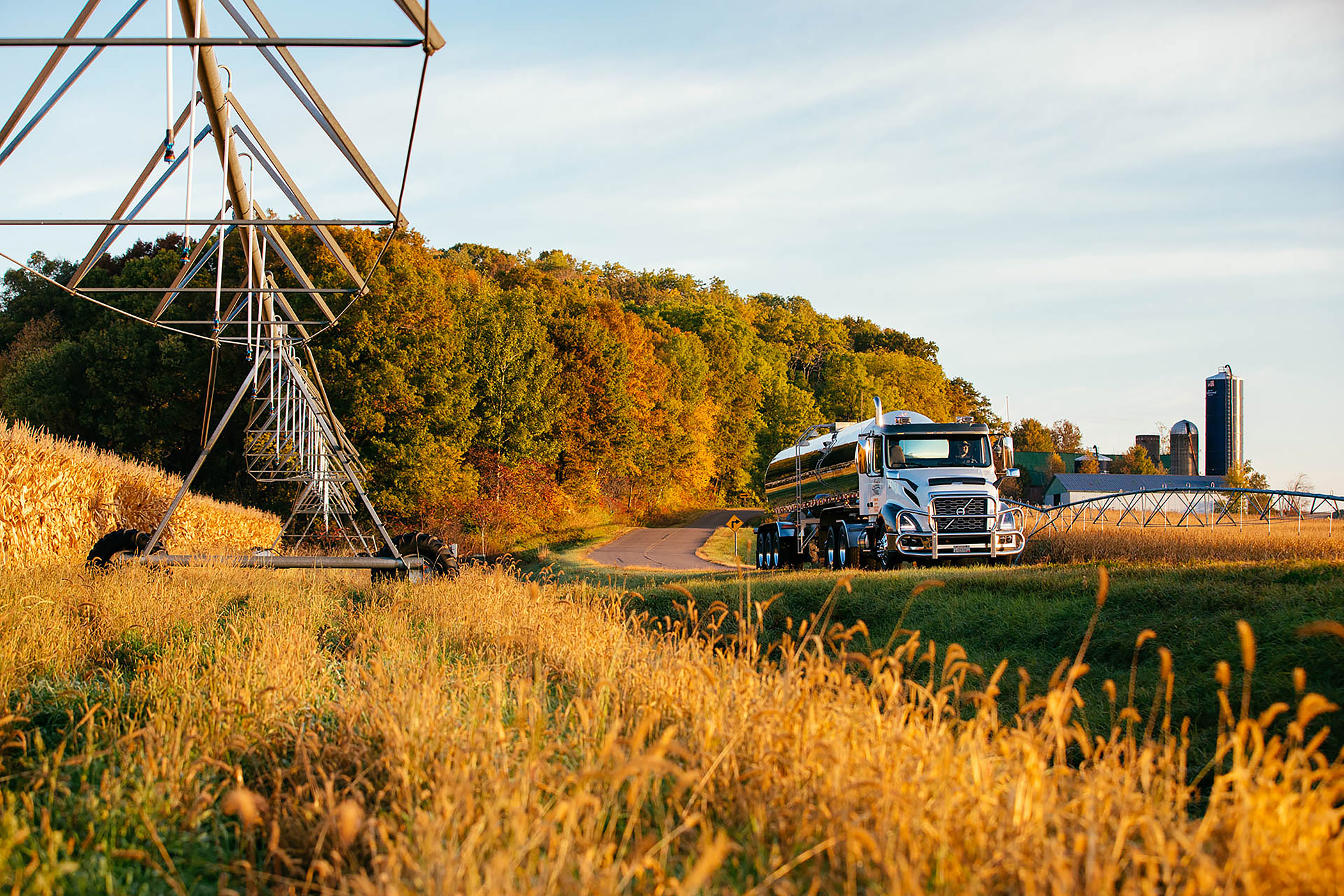
Streamlining the Milk Hauling Process
By Maura Keller
When it comes to hauling milk from milk producers to milk processors, streamlined efficiency is the proverbial “name of the game.” Just ask Peter Lemke, co-owner of Lemke Bros. Trucking, a Wisconsin-based milk hauling company that has recently partnered with McFinn Technologies to install a series of McFinn’s Bowpeller pumps in the seven dairies that Lemke Bros. serves.
“In the dairy industry, when you are pumping raw milk to haul to the processor, it’s all about the time it takes to complete the job. You want to try to save as much time as possible as it really can impact the amount of milk you can haul each day,” says Lemke, who, along with his brother Chris, are third-generation milk haulers. Established in 2009, Lemke Bros. Trucking began when the two brothers decided to continue their father’s and grandfather’s legacy, hauling milk around north central Wisconsin.
Back when their grandfather began hauling milk in 1948, the process involved carrying 100 lb. cans of milk from the milk house to the truck. Luckily, advancements have been made in the industry, thanks in part to McFinn Technologies’ state-of-the-art pumping technology. Specifically, McFinn’s Bowpeller pump is dramatically impacting the milk pumping segment of the dairy industry. The Bowpeller boasts a two-stage, high-efficiency casing that ensures fluids don’t linger, while gently handling pumped fluids, minimizing shear and emulsification and offering the utmost in pump control. The innovative features of the Bowpeller pump ensures high efficiency performance across varied temps, resulting in a long seal life.
So why did the Lemke brothers decide to install McFinn Technologies’ Bowpeller pumps on the dairies they serve? Quite simply, to save time. As Lemke explains, his company has seven trucks and in Wisconsin, they can legally haul 67,000 pounds of milk per trailer.
“That’s always our goal – to make sure we’ve got full, efficient loads,” Lemke says. “When we work with a large dairy farm, we may be taking three loads a day. But the problem is that when you have trucks with pumps directly on them, you run into a lot of problems including maintenance and cleaning. You have to take these pumps apart every day and thoroughly clean them. So we decided to install a Bowpeller pump at one of the dairies to see what difference it could make. And we found it was saving us at least 15 minutes to load a trailer and in the case of a dairy where we are hauling three loads a day, that is saving us close to 45 minutes of pumping time. In our industry, timing is everything, so this had a huge impact on our operations.”
In addition, with the pump being on the dairy farm, a milk hauler no longer needs to have a pump directly on the trailer, which opens up available weight and allows the company to haul more milk.
“We also can back up to a dock because we don’t even need a hose in the back of the truck,” Lemke says. “We just make the hook up inside and away we go. It’s very convenient. Also the pumps can be set up to clean themselves, or clean the silo or bulk tank. So they save space, they stay super clean and there is no maintenance. You no longer have to mess around taking pumps apart, which requires so much time.” Also, transitioning from pumper trailers to transport trailers also offers significant cost savings for the milk hauler.
Since the first installation, Lemke Bros. has Bowpeller pumps at all seven of their dairy customers – this includes farms with as few as 150 cows to large-scale farms with 4,000 animals.
Van Der Geest Dairy in Marathon County, Wisconsin is one such large-scale dairy where Lemke and his team incorporated Bowpeller pumps into their operations. Milk storage and cooling systems are significant capital investments for large-scale dairy producers, including those that utilize direct tanker loading (DTL) systems, where chilling plates are used to keep raw milk cooled in tanker trailers. Depending on the size of a dairy farm, producers that utilize DTL systems, may have higher hauling costs, due to the need to have several trailers on-site at all times.
“On a dairy farm where they ship four or five loads of milk per day, with direct ship tankers, here’s the problem: When the tanker goes to the dairy, they have to agitate it and sample it, and wash that tanker every time before you can take it back. But with a milk silo, we can haul as many loads throughout the day and only have to clean the tanker out once,” Lemke explains. “And with the Bowpeller we can load a trailer in 17 minutes.”
So, rather than using a DTL system at Van Der Geest Dairy, Lemke Bros. proposed installing two milk silos, along with McFinn’s Bowpeller pumps, and servicing the farm with one truck that could haul several loads, rather than investing in five or six tankers that would be sitting on the dairy farm. Each silo at Van Der Geest Dairy holds 330,000 lbs. of milk, or 40,000 gallons; they haul out four to six loads of milk a day. Each tanker hauls 67,000 lbs. of milk. From the time milk leaves the cow it takes three minutes for the temperature to change from 101.5° to 34°. and into the silo. And with the Bowpeller pump, it is loaded at more than 4,000 lbs/min.
“By using this system, we’re not agitating or washing repeatedly throughout the day, losing time,” Lemke says. “It’s totally worth it as we really want to stay away from the direct ship because it’s so time consuming.”
Lemke Bros and McFinn Technologies are true partners in striving to streamline the milk hauling process. “You could call anytime and they are there to help, which is especially important when you are installing the pumps on the farm. They help you. To me, it’s the way to go. It’s just so much faster, it’s so much cleaner. You can utilize the equipment more because you’re not tying up trailers, which are meant to be moving, not sitting.”