Improved Feeding Technology in Today’s TMRs and Bale Processors
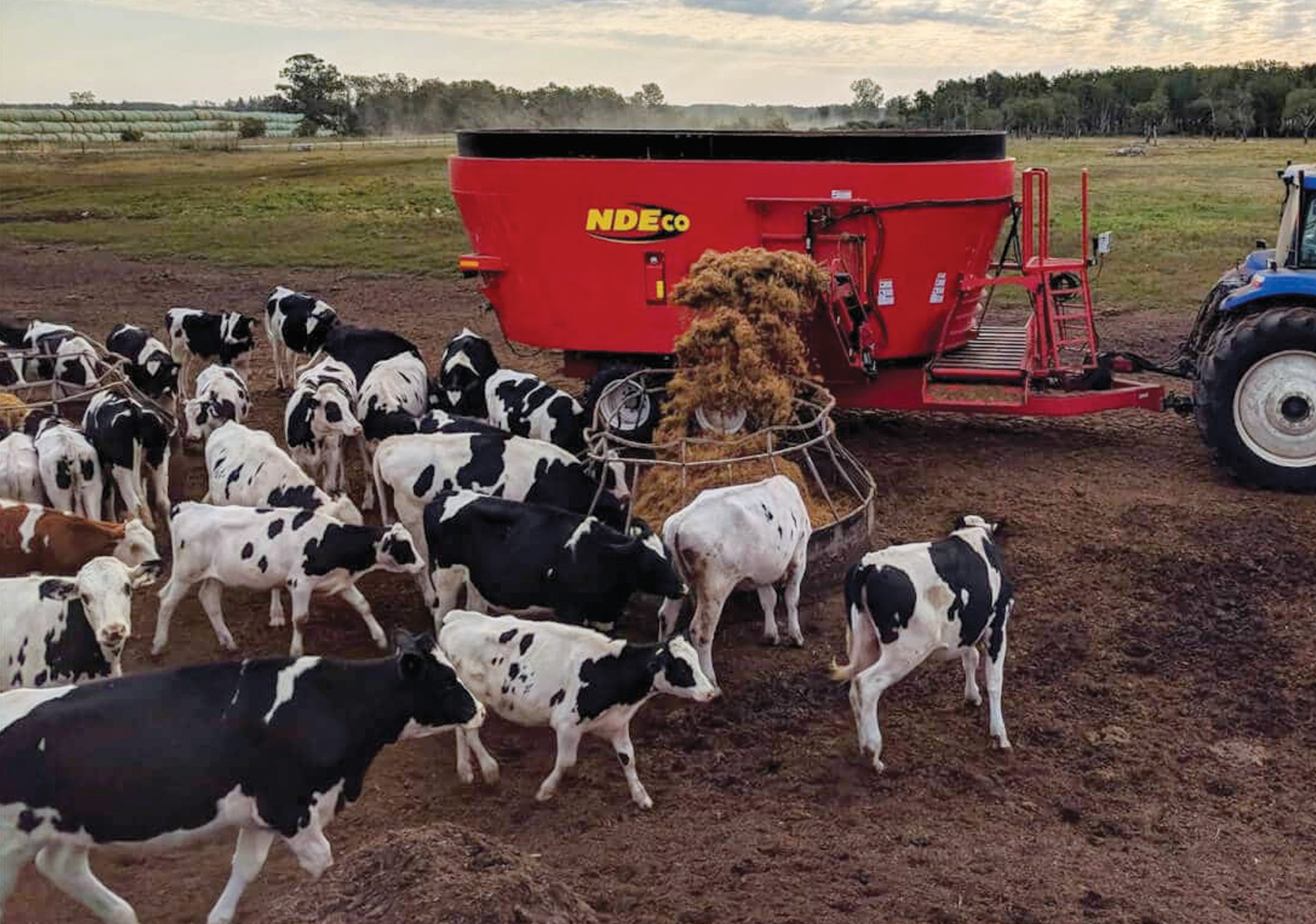
Improved Feeding Technology in Today’s TMRs and Bale Processors
By Maura Keller
Total mixed ration (TMR) mixers and bale processors are core components of today’s dairy farm operations. TMR mixers provide exact variations of feed for livestock rumen health, while improving feeding efficiencies and ensuring animals are getting the nutrients they need in ration levels that are appropriate. Likewise, bale processors help reduce the percentage of waste in today’s feeding operations.
As sales Joshua Stucky, sales manager at Fair Manufacturing explains, in recent years, the advancement and evolution the industry has seen in technology has been impressive. Producers can now customize how their equipment performs to fit the specific needs of their operation.
“We are no longer just using technology to steer our tractors,” Stucky says. Fair Manufacturing Inc. has been in business since 1963, and specializes in snowblowers, bale processors and hay rakes. Fair has been at the forefront of the equipment, livestock and hay industries for decades.
“As a manufacturer of ag equipment, they always strive to be a leader in innovation and technology, to provide the best possible equipment to customers and support growth within the industry,” Stucky says. Fair Manufacturing produces 7830-TD (Top Discharge), and wheel loader mounted 7200-LMH for the bale processing world.
“Technology doesn’t always mean electronics. Manufacturers are using scientific data and knowledge for practical purposes as well. We are learning how to build equipment better,” Stucky says. “Equipment built with specialized knowledge leads to designs that operate more efficiently and are a lot safer than what we were using in the past.”
Fair’s patented ejection and access door allows operators to safely eject unwanted materials and access internal components without having to enter the machine. Bolt in stationary knives process hay into smaller pieces, making it more palatable for livestock, and capable of being fed directly from the processor.
According to Franco Banman, operations manager at NDEco was established in 1998 in Sioux Falls, South Dakota, known then as NDE/New Direction Equipment. NDE partnered with Hi-Tec Industries Inc. in Manitoba to build its very first vertical feed mixer. After a strong start in the mixer industry, in 2003 NDE was bought by the owners of Hi-Tec to grow the business and continue manufacturing the best vertical mixers on the market.
“NDEco is a longstanding supplier in the livestock industry, renowned for its range of vertical total mixed ration (TMR) feed mixer wagons, truck mounts, and stationary mixers,” Banman says. “Our offerings include vertical TMR mixers ranging from 330 to 1700 cubic feet in capacity, in the form of single auger, dual auger or triple auger designs.
As Banman explains, NDEco’s auger is the key component for producing a uniform and consistent ration throughout the mix from bottom to top. It features a design with full flighting on a continuous curve, which provides the best lift action and ensures that once feed material is picked up, it moves up in a uniform and consistent manner, rolling material back into the mix evenly and not dropping material in batches that create an uneven ration throughout.
“Not only does this create a more uniform ration, it also speeds up the processing time by working harder to ensure once feed is picked up it keeps moving with maximum efficiency,” Banman says. “Being aggressive with the design focuses on the best possible mix at the fastest possible pace with the largest possible material load, directly converting the required horsepower into the result of the mix.”
To match the aggressive auger design, each NDEco auger has the capacity of up to nine large knives, including industry exclusive carbide options designed to aggressively slice through bales and roughage.
Dr. Alan Vaage, Ph.D., ruminant nutritionist at Jaylor, explains that Jaylor manufactures single and twin auger vertical mixers in capacities from 50 to 1250 cu. ft. to meet the needs of farms of every size. Jaylor also manufactures heavy-duty, four-(patented, spiral) auger mixers for the feedlot industry. Jaylor has been manufacturing TMR mixers for over 30 years since 1993.
Jaylor also has over 32 patents and patents pending for innovations on their machines. Of special note is its patented “square-cut” auger with which Jaylor machines process long forage into a uniform mix that resists sorting in as little as half the time as other TMR mixers. This includes the “square” edges of the auger, the sloped top, patented Alexander Knives (45-degree knives that under-cut the bales) and vertical knives on a slide plate that loads the auger and has a patent for 20% lower power requirements.
“Producers need to identify their needs in relation to the size of mixer they require – the number of animals to be fed, number of times TMR is to be fed, number and the size of bales that need processing, etc.) It is best to work with a reliable retailer who can help identify the best model for a particular farm,” Vaage says.
Marloo Equipment offers a range from 350 CF to 2500 CF TMR mixers. Wouter Vanloon, owner at Marloo Equipment says there are several factors to consider when selecting TMR mixers including size groups, barn height and widths, loader dump height, and HP requirements for the TMR mixer.
Continuous Evolution
In recent years, technological innovations surrounding this equipment has evolved over the last several years. Recently, the focus has shifted towards reducing fuel consumption while maintaining mix consistency.
For example, NDEco’s auger design, combined with their industry-exclusive aggressive 24” carbide knives, ensures quick and efficient feed processing.
“Our unique stepped floor design enhances mixing consistency from front to rear, surpassing other designs,” Banman says. “Additionally, our doors are the widest available, facilitating efficient feed delivery. There is also a growing emphasis on feed management and tracking, prompting us to offer scales and accessories from three different manufacturers to accommodate any farm’s feed management software needs.”
Dan Boecker, sales person at Dairyland Supply, says today the industry has new software to better track feed, manure application, and animals. “These tools help make the right day-to-day decisions for profitability and sustainability,” Boecker says.
When Boecker works with producers who are looking at selecting and purchasing bale processers and TMRs, Boecker likes to start by look at what the work load is being done, and match it with a unit that can stand that work load.
“Then horsepower is an important factor, and also mix quality to match the ingredients being fed,” Boecker says. “Last but not least, the company behind the product is the most important of them all. The dealer cannot support the product without support from the OEM. These great companies can create trade value down the road, and make owning a machine make sense.”
When producers are selecting bale processors and TMRs, Banman says they should start by considering their ration composition and farm layout. A high-roughage ration with round bales requires a different mixing chamber and knife setup compared to a mix consisting mostly of processed feeds.
“Other factors to consider include loader size, the distance from feed storage to pens, and feed group sizes, which will influence the choice of tub capacity and conveyor setup,” Banman says. “Collaborating with a knowledgeable dealer who understands the operation can greatly assist producers in selecting the best equipment for their farm, as every farm has unique needs. Consistency is key. Maintaining a consistent ration in front of the animal is crucial, and a reliable machine, along with proper mixing procedures, makes this achievable.”
When making a bale processing purchase, Stucky says it is important to recognize that plain and cheap aren’t always the best options. Downtime caused by poorly made products with cheap components will cost you more than just dollars in parts.
“Buy good quality equipment from a manufacturer with a reputation for building tough, durable products, and that has a history of longevity and great customer support,” Stucky says. “These options are beneficial to any operation, of any size. Equipment may seem costly up front but when used and maintained properly, it can pay for itself and protect your bottom line. You have to look at the big picture. Put pen to paper. Think of the things that others do not.”
In addition, Stuckey says producers should make sure that they are purchasing the right piece of equipment for the task at hand. Is your purchase designed to do the job you bought it for efficiently, or just do the job?
“Time is the most valuable asset of any operation, because you cannot create or purchase more of it,” Stuckey says. “If you process 10 bales a day, and your machine and process take six minutes per bale as opposed to the proper machine and a process that does it in three, it will cost an extra 182.5 hours annually. That’s 182 hours of payroll, 182 hours of fuel, 182 hours on your machinery.”
In addition, to ensure optimal mixing performance, it’s important to regularly maintain items like knives and the kicker plate at the bottom of the auger. The kicker plate should be replaced when it begins to wear as it has a bigger effect on the quality of the mix than most realize. Additionally, routine greasing, planetary oil changes, and daily circle checks will keep your mixer running efficiently.
Vaage adds that other common mistakes producers made as it relates to TMR and bale processor selection includes buying too small a mixer trying to save money, buying too large a mixer for feeding smaller groups on the farm leading to poor mixing, continuing to feed concentrates separate from the TMR, and not working with a nutritionist to determine the most appropriate ration mix to be fed.
VanLoon at Marloo Equipment often sees the wrong ingredient order that goes into the TMR mixer – for instance, heavy ingredients sink and light ingredients float.
“You have to consider the physical properties of the ingredients used that affect mixing, density, size, water absorption capacity. Mixing time after last ingredient is also a factor,” VanLoon says.
“TMR rations enable each cow to consume the ingredients and nutrients they require for a balanced ration,” Vaage says. “This generally enables higher production and optimal health, but only if ration is resistant to sorting.
Stucky points out that with the cost of feed and inputs on the rise, producers have learned the importance of delivering nutrients to their livestock in an accurate and efficient manner. New advancements in equipment manufacturing have resulted in providing better quality feed for animals.
“If producers can make better quality, more palatable feed and deliver it in a more precise way, they can deliver more nutrients per pound of feed. Better mixing and blending technology have led to a more consistent ration of nutrient dense feed,” Stucky says. “That means every animal is consistently getting the nutrients they were intended to.”