Robotics Can Save Labor and Enhance Dairy Cow Management
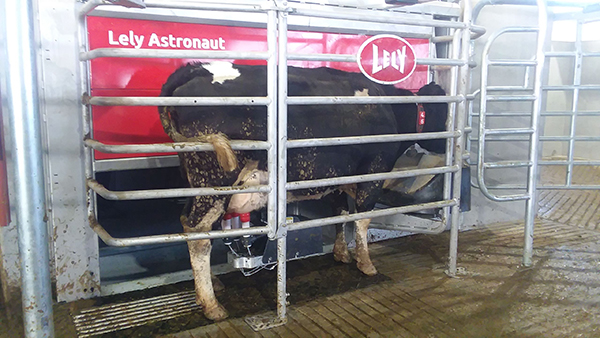
By Heather Smith Thomas
Robotic milking technology (Automatic Milking System) was developed in Europe to address labor issues on dairy farms and became available to European dairymen in 1992. This technology was introduced to the U.S. in 2000 and gradually came into use in various states. For instance, a few dairies in Michigan began utilizing robotic milking in 2009.
Robotic milking is a voluntary milking system that allows cows to set their own milking schedule. The robot milks the cow, so the dairy farmers have more flexibility in how they use their time–with more time for farm management or other activities. Automatic milking systems collect information on milk quantity and quality and cow health, which also helps farmers better manage their herd.
The cows voluntarily enter a robotic station to be milked when they want to be milked, and the farmers can collect valuable data on each cow’s milk production, health, and overall well-being. Each cow wears an electronic collar that allows the robot to identify her and track her health, diet and milk production. The robot cleans the cow’s teats, then uses lasers to locate each teat and attach the milking cups. Cow receive a nutritional supplement based on their milk production. As the cow is being milked, the robot analyzes the milk and creates data.
The milking robot supplies information unobtainable in a conventional dairy situation, making it possible to manage animals at an individual level. Management by exception is the new method; the dairy crew can concentrate on the cows requiring attention. With the milking robot, it is possible to supply an individual cow with all her needs for optimal health, production and well-being, without the extra labor. Here are a couple of examples of how certain dairies have made use of robotics.
TEXAS DAIRY – A dairyman near Windthorst in northern Texas decided in 2022 to switch to robotic milking and at that point in time was one of only six robotic dairies in the state–most of them in that region of north Texas.
He started using robotics because his milking parlor was old and outdated and also because he wanted to be able to get the full genetic potential from his cows. He was averaging 80 pounds of energy–corrected milk before switching to the robotic milkers, and within a year was averaging 95 pounds of energy–corrected milk per day. An energy-corrected pound of milk (ECM) is a calculation that estimates the amount of energy in milk based on its fat, protein, and volume. ECM is adjusted to a standard of 3.5% fat and 3.2% protein.
He installed nine robots in a climate-controlled 100,000 square-foot tunnel vent barn—a cooler environment for the cows during hot Texas summers. The robots capture data through rumination collars the cows wear; the collar provides continuous monitoring of movements and rumination and are essential for the robotic milkers because they communicate with the robot about the cow being milked. The robot reads the cow’s collar and provides the farmer with information such as heat detection, health and how much milk the cow is producing.
The robot reads the collars as the cows come in to be milked, and if a cow has been in there less than four hours ago, it automatically kicks her out because it is too soon for her to be milked again. In this particular dairy, the cows willingly come to the robots for feed pellets. Depending on how much milk the cow produces, the robot determines the amount of pellets the cow is allowed to have.
The robotic milkers work continually, 24 hours a day, allowing the cows to come in as they please and as often as they want. Every cow gets milked at least twice a day and sometimes up to five times a day if the cow wants to. Each robot can handle 60 cows and has allowed this dairy to grow from 450 cows to 550 with one less employee.
The cows seem to like the robots because they’re never stressed with a too-full udder. If they’re coming in three or four times a day, a high producing cow is more comfortable and less stressed than she would be if she was only being milked twice or even three times a day in a traditional parlor.
The cow’s teats are cleaned with a brush and disinfectant and then a laser reads the cow’s teat placement before the robot connects to the cow’s teats. When the milking is finished, the teats are sprayed with a dye that protects the teats, the cow is released back to the herd, and the next cow comes through. In this particular dairy, there are usually two to three cows waiting to enter.
The robotic milkers have increased each cow’s production and allowed the farmer to do other tasks and spend more time with his family. He feels the biggest benefit of this technology is the fact that sometimes on a dairy you have human error, and the robot eliminates that. He can go to his computer at any time during the day or look at the app on his phone and see if a cow is sick or has any kind of problem.
IDAHO DAIRY – David and Natalie Nelson are on a dairy farm near Preston, Idaho—on land that was homesteaded in 1888 by David’s great-grandmother. There have been a lot of changes over the years and the farm was transferred to David and Natalie from his parents in 2019. They built a new barn five years ago and put in robotics for milking.
The new milk barn has space for 240 cows. “We started with three robots and left space for another. We put our fourth robot in a year and a half ago and were able to buy more cows and heifers and grow the herd to 240 milking cows,” David said.
“The cows catch onto the robotic system pretty fast. The heifers learn quicker than the older cows. They come in for the food they receive during the milking. The food entices them, but they can come in as they wish. Our cows average about 3.2 milkings per day. If a cow tries to come too soon, however, like if it’s only been a couple hours since she was milked, the robot won’t milk that cow and will let her back out—instead of trying to milk her every time she comes.
“We want a minimum of 20 pounds of milk each time, but it depends on where the cow is in her lactation,” Natalie said. A fresh cow that’s producing a lot of milk might get milked up to 6 times per day, but when a cow is near the end of her lactation and getting ready to be dried off she might only be milked once or twice a day.
“That works for us and is also better for the cow. A high-producing cow at the peak of her lactation needs to be milked more often than two or three times a day. She gets to choose the frequency.”
This is healthier for the cow and also improves milk production for the dairy, as well as saving labor. This system has been a great improvement for dairy management.
“Lely, the company we chose to go with for our milking robots, has been in the milking robots business for 30 years. The first Lely robotic milking machine was introduced in the US in the year 2000 in the Midwest. We started seeing robotic milking machines come into our area about 8 years ago and we started looking at robotics because we were working on the transition of our farm from one generation to the next and trying to figure out where we wanted to be in the future. Our barn was really small and old so it was time to do some kind of change,” she said.
It was either stop dairying or build a new facility. “We had to decide what we should do, and our original plan was to build a new conventional parlor. Then we learned about robots,” David said. “We went on a few tours to look at them; we went back east and to several different dairies to see how they worked and whether they would fit for us. We made a plan to go forward with this technology.”
It was a little scary because it was a large investment, especially when they were planning to start over completely with a new facility. “We haven’t regretted this decision because it has increased our production and I think the cows are healthier,” Natalie said.
“With the robots we get a lot more information about the cows and their health,” David said. “They wear the tag, so we can track the cow, and can also see if she’s starting to get sick, even before she shows any symptoms. We are able to be proactive and can have a better outcome if she has mastitis or some other problem.”
This allows the cows to be in a more natural environment and do things more like they would do on their own. “They can set their own schedule, with fewer disruptions from people.” A dairy cow is very specialized, and anything a person can do to help her and keep her comfortable and content is much superior to some of the ways people handle cattle.
“The robots and all the information they give us can help us to be more consistent, and cows love consistency!” Natalie said. They are creatures of habit and happiest when they are accustomed to something rather than confronted with something new and scary. The milking is consistent every time and robots don’t have a bad day or give off bad vibes. Cows can sense when a person is upset or having a bad day.
“When David started looking into robotics we decided this would be the future for us.” It will also be helpful for other young people going into dairying because it will make their tasks easier.