Baleage Advantages
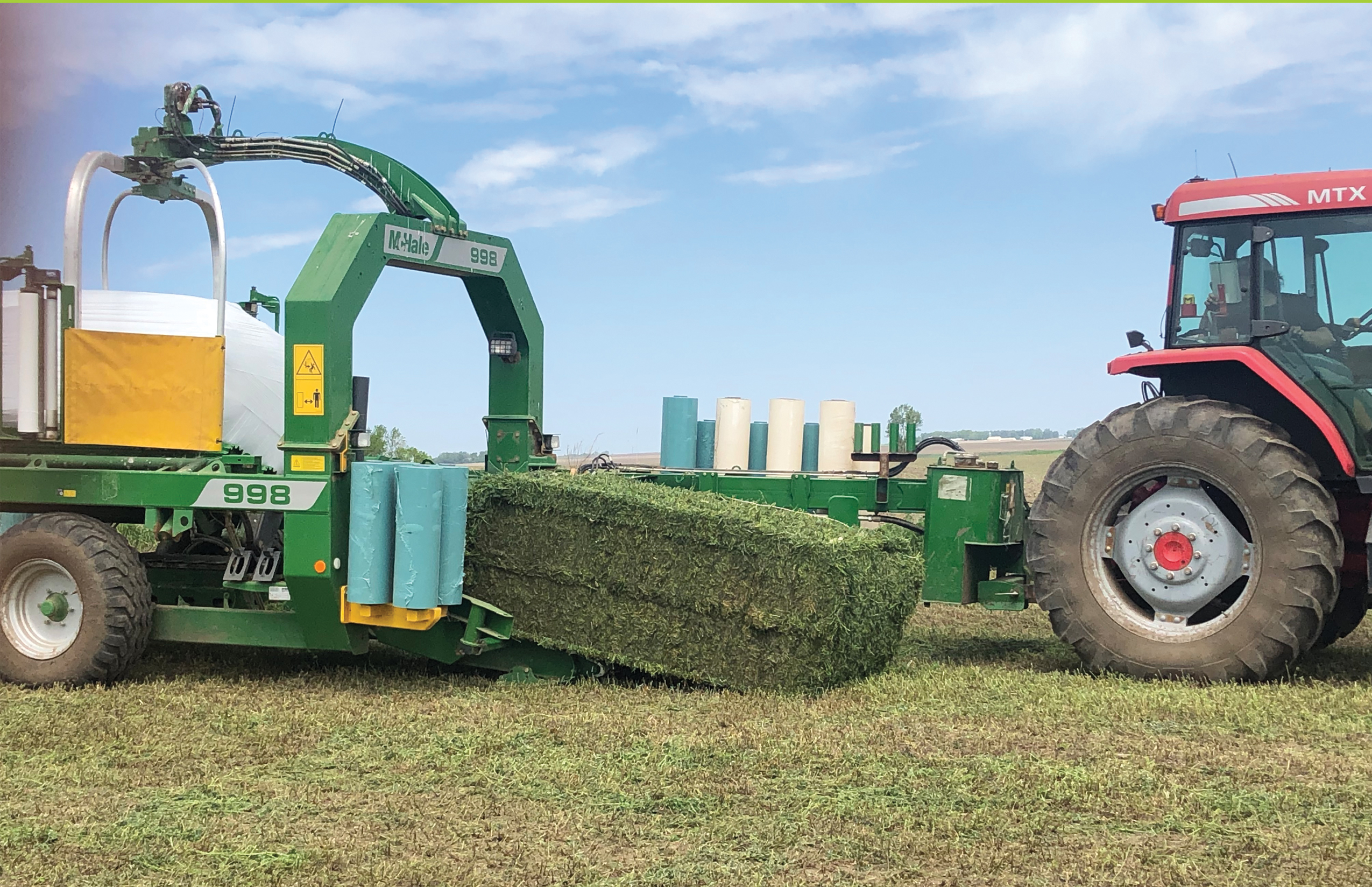
Baleage Advantages
By Heather Smith Thomas
Silage in piles, pits or silos has been the traditional way to store forage harvested wet–compacted and stored in airtight conditions, fermenting. In recent years, several methods have been developed to wrap silage/haylage in airtight bags using plastic film. Harvesting and storing it this way can capture nutrient quality of forages without the losses often associated with trying to get it dry enough to bale and store without mold. Animals with high nutritional requirements such as lactating dairy cows and young, growing animals often perform better on good silage/baleage, and this can be a way to harvest and store good feed without trying to dry it during wet weather.
Evolution Of Baleage
Baleage technology has advanced dramatically in the past 15 years from a cost standpoint and improved transportability. The wrap (plastic film) can be used for individual bales or in a long tube, but there are many different types of wrappers. The tubes may not have many advantages over bagged or bunker silage, depending on your situation, and bagged silage has some advantages over poorly bunkered silage.
Baleage is a bale that is put up wet and then wrapped. Bagged silage is a chopped feed (silage) compacted into a bag as opposed to being stored in a silo, pit or ground pile. Baleage may be preferable in many situations as a supplemental high-protein forage like alfalfa and may also be the best way to capture some supplement-quality hay like wheat or oat hay in wetter climates. Traditional silage can be put up cheaply but spoilage losses are often high, adding to the final cost. Silage also requires different equipment to feed than baleage for an operator who already uses bales.
Bill Godfrey, a farmer in Oklahoma, prefers baleage. “A few years ago one of the local farmers bought an in-line wrapper and several producers here are now putting up baleage though some of them are also still using silage. Farmers here primarily use dry hay,” he says.
“I am more concerned about quality rather than volume of forage, whereas beef operations are more interested in volume. They can get by with less quality and can also supplement if necessary,” says Godfrey.
There are opportunities now to put up good-quality forage as baleage. “This is a two-fold advantage. It us a quality product and harvesting is not weather-dependent. This is a big concern if you are putting up a large quantity/tonnage product. When you look at harvesting equipment today, there has been a big change. Fifteen years ago, John Deere and New Holland both had something they called a silage special that was a round baler, but only a few companies were making and promoting equipment for baleage. Today all the machinery manufacturers have multiple products for baleage. More producers are worried about quality,” says Godfrey.
“For producers in my area, transportability is a key concern. We all have pastures with cattle scattered everywhere. Running a TMR (total mixed ration) mixer on a big truck does not make sense like it does for a farm where all the cattle are in one location. One concern regarding harvesting wet forage is that you are storing and hauling something that is 50% water. “A 5-by-5 or 4-by-6 bale of baleage weighs about a ton, using the new equipment. Even if it is 50% moisture (or less, if the farmer uses a preservative and gets it down to 45% moisture) and only 1000 pounds of dry matter, the quality is so much. You have a high-quality product that costs more to put up and store but requires no supplementation, and in the end may be cheaper,” says Godfrey.
All forage crops contain a certain percent water. When talking about transport, this becomes a factor if you are hauling a lot of water. Yet many crops are difficult to harvest as dry hay and do it effectively. In some climates this is almost impossible. In that situation baleage is great because you can utilize many different crops and crop mixes that you would not be able to harvest any other way.
Minimizing Dry Matter Loss And Spoilage
Dan Funke has a cattle operation and also harvests and sells baleage in northwestern Iowa. “One of the biggest struggles in producing forage, no matter how people harvest or store it, is dry matter loss. “There are many places in our process of harvesting that we can minimize that loss. A lot of people do a very good job of growing a crop but end up losing half of it (at various stages) whether through poor harvest management, storage, or during feeding. I think it would alarm people to realize how much they are losing,” he says.
“As we’ve gone through this learning curve we’ve found that density is important. If you are harvesting silage and packing it in a pile, there are formulas to make sure your packing density is high enough. It involves having enough weight (of tractors) on the pile at any given time in relation to how fast the feed is coming in,” he explains.
“We’ve noticed the same thing with baling and wrapping. We started with a standard-density baler and went to a high-density baler, and then a super-high-density Krone baler. The more you can compact feed, the less oxygen will be in it, and the better it will be. A super-high-density baler is not for everyone because it is very expensive, but you must do everything you can to make sure bale density is high enough. A loose bale will be subject to losses, and some potential spoilage. Most of our baleage goes to dairies, where quality is extremely important,” Funke says.
“The key thing people need to remember is to use enough high-quality film. You have one chance to get this right. You spend money to bale the feed and then wrap it, and a few dollars more for a roll of good quality film can make a big difference; this is not a place to cut corners.”
He learned this early on. “People call wanting me to try their brand of silage film, but it hasn’t worked very well for us to experiment in that area or cut corners. If you don’t apply enough film you’ll have losses. Typically it takes 8 layers, and it might cost a little more but ensures good feed,” says Funke.
“The only time we put less film on is at the start of the season when our supply of old crop is low and the new crop won’t be stored long. We may just put 6 layers on when we know it will go right to the farm and get fed within a week,” he explains.
“Many people want to save money, but the wrapping process is not a place to try to save money. The same applies to making a silage pile. People who don’t cover their piles aren’t very good with math, because when you figure what it costs to cover it versus the loss of feed, it’s a no-brainer. Covering properly is important; you need to get enough plastic on and get it weighted down properly,” he says.
On a dairy the tolerance for spoilage is zero and dairymen have learned how to accomplish this. “When they peel that plastic off, the feed is absolutely perfect. I realize that not everyone needs perfect feed, but the cost of getting it perfect is far less than the cost/loss of not taking care of it. It amazes me that people don’t want to spend the money to put a cover on it. They worked hard to grow it, and even harder to harvest it, and now it’s in a pile and they let it deteriorate from the top down,” says Funke.
“I compare it to harvesting corn. If you were driving your combine through the field and 20% of your crop was coming out the back and landing on the ground, you’d do something to fix that combine. So why are people complacent about forage losses?” The cost is just as big, if not bigger. When harvesting forage, the key is recognizing where your losses are, and doing everything you can to minimize those losses.
John Hall, PhD (Extension Specialist, University of Idaho, Superintendent of the Nancy M. Cummings Research, Extension and Education Center) says there is a growing interest in baleage, and this interest generally stems from weather challenges when harvesting forage. “Here on our ranch we can usually get 2 cuttings of hay but it’s a lucky year when we ever get a 3rd cutting that can be made into hay. We often have too much fall moisture,” he says.
“If producers want to make baleage they need to do some homework and need to understand things like wilting times and how much moisture to end up with. Most of our moisture testers for hay don’t go up high enough. There are some methods that work, but you need to have the right tester. Learning how long you need to dry it on a certain day, to get down to 50% moisture, is crucial. It might be just a few hours in the heat of summer or it might be just overnight in a cooler time of year,” says Hall.
Moisture level is crucial because if it’s too dry it won’t ensile and will mold. If it is too wet you lose a lot of yield; the material becomes runny and slimy with too much liquid. “A lot of the soluble carbohydrates end up in the fluid and can be lost,” he says.
It takes a while to learn how to do it properly. “If someone you know is already doing it, spend a day with them to learn the finer details,” he suggests.
The disadvantage of baleage is the challenge of transport if you have to take these bales very far to feed them. They are heavy because of all the water in them. “Whether or not they are feasible depends on how far you have to take them and how you are using them,” Hall says.
Tubes Versus Individual Bales
“The advantage of the inline method is that it is much faster and takes less plastic because they are only wrapping the sides of the bales,” says Hall. “These are expensive machines, but they can be shared between farms because most of them have wheels and a tongue that goes on them and they can be hooked behind a pickup and taken to the next place. Several farmers could share the cost this way,” says Hall.
“The individually wrapped bales will keep and not spoil,” says Godfrey. “The tube-line is half the cost on plastic wrap but to tube-wrap you need to put in more than 50 bales because the first two and last two will be dry bales, unless you use an end cap. You really need to do 80 to 100 bales to make it worthwhile unless you use the end caps.”
When you open up the tube to feed, the exposed hay starts to spoil, especially in summer when weather is warm. “In winter you can get by for a couple days without much spoilage loss. Some guys smash a dry bale onto the exposed end, but there will still be some spoilage–but less than you’d have on a silage pit. If you are going to do in-line baleage you should do long rows, to reduce waste,” he says.
“My biggest concern is forage quality. I could probably get away with doing tube-line but I do some baleage of winter annuals crops, baling and wrapping in May-June. We’ll also have a summer forage that we’ll bale and wrap later, and possibly a late summer crop that we don’t bale until fall. I am not doing all of mine at one time. The argument for tubes is that they are the most cost-effective if you are doing 500 or more bales per year, and for my operation this would probably work and be cheaper, but I’d either have to buy or rent a tube-line wrapper or hire someone with a tube-line wrapper to come wrap bales on my schedule for harvesting. Perhaps on the harvesting side the tube-line makes the most sense, but on feeding it out I am not sure it does. I like the individually-wrapped bales and the fact you can stack them, and if you are going to sell some, they are easier to transport—versus cutting them out of a tube or row. In the winter you might get by without feeding it up immediately but in summer you can’t,” says Godfrey.
Funke individually wraps every bale he puts up but says there is also a place for in-line wrapping. “For many reasons it is not a good solution for us, and the challenge of transportability would be the main reason. I sell 95% of what I bale so it must be transportable. It’s not that you can’t transport in-line bales, but you have to take them out of their package to do it. There are several advantages to individually wrapped bales. If you get a hole in the wrap film it will only ruin one bale and not a whole bunch of bales.”
One of the issues with wrapped bales is vermin and coyotes. “Mice can get into them and then the coyotes go after the mice and then you have holes in the wrap,” says Hall. “In our area, elk can also be a problem, tearing into the bales.”
One of the disadvantages of the inline system is that you can’t stack the bales, so it takes a lot of space to store them. “If you are in an area state where you don’t have elk, you may be able to just put them out along the edge of a field,” Hall says. Every situation is unique and will determine which method you ultimately choose.
More Nutrients And Less Waste
Godfrey says baleage is more expensive to harvest, but provides more flexibility—to be able to put up wet forage and have it stored with no loss of quality.
“Cows often pick and sort through dry, coarse hay and waste some. With baleage, if you put it up right, they don’t waste any. With dry hay, like a sorghum/sudan crop, cattle might pick through it and leave the stalks and you end up with a lot of waste. You can chop it and put it through a TMR mixer, and from a cost standpoint that’s the cheapest way. The feed is cheaper, but what does it cost to run a big truck all day that only gets 4 miles to the gallon and costs $100,000 to purchase? It works for a big centralized operation, but not for cattle that are spread out,” he explains.
“When done properly baleage creates a fool-proof feed,” says Funke. “The cost of wrapping is always and easily offset by the increase in quality and quantity. If you can’t justify the equipment yourself, you can hire someone to do it—if there is someone in your area who does this. I drive down the road and see people trying to harvest dry hay and it’s getting rained on and turning to junk. People work hard to soil test responsibly and grow a good crop and take care of it and get it cut down, but then it ends up in a downward spiral with one loss after another,” says Funke.
Silage Versus Baleage
Traditionally silage is an energy crop like corn or sorghum, whereas baleage is putting up a hay-type forage. “Some people have tried doing corn silage as baleage but you have to use more plastic wraps because the stalks poke holes in it otherwise,” says Godfrey. “It works, but from a cost standpoint if you’ve always had a silage operation and have the equipment it makes sense to keep doing it. With some of the grasses and forage sorghums or even triticale or rye, or winter annual cereal grains for stored forage, it may make sense to chop and bag them as opposed to cutting and putting them up as baleage,” he says.
“It all depends on your situation and operation. If you already own the haying equipment, like many people in our area do, when you upgrade hay balers you might buy one with cutter knives that is set up to do baleage. You can simply lift the knives and do dry hay also. Then you need to buy or rent a wrapper,” Godfrey says.
Funke says traditional silage can be put up cheaper than baleage but there can be tremendous spoilage losses and it ends up not being that cheap. “A silage pile can be challenging to keep, depending on how much a person uses. Having an open face on the pile in winter is not a big issue, but in the summer—with warmer weather—it can ruin quickly if you’re not feeding it fast enough. In that situation you are never feeding good feed. You are always feeding what has spoiled on that open face,” he says.
On a smaller operation, this would be a key factor and baleage would be more cost-effective/economical than silage because each individually-wrapped bale is fresh, perfect feed, every day.
For smaller producers baleage can be done cheaper and more effectively than silage, with less forage loss. “It would be a win for them, over trying to make dry hay and/or silage. Every situation is different, however. Some people have a storage facility such as a bunker or an upright silo they can utilize, and that’s a great way to store silage, though silage in piles/banks isn’t bad,” says Funke.