Today’s Parlor Designs
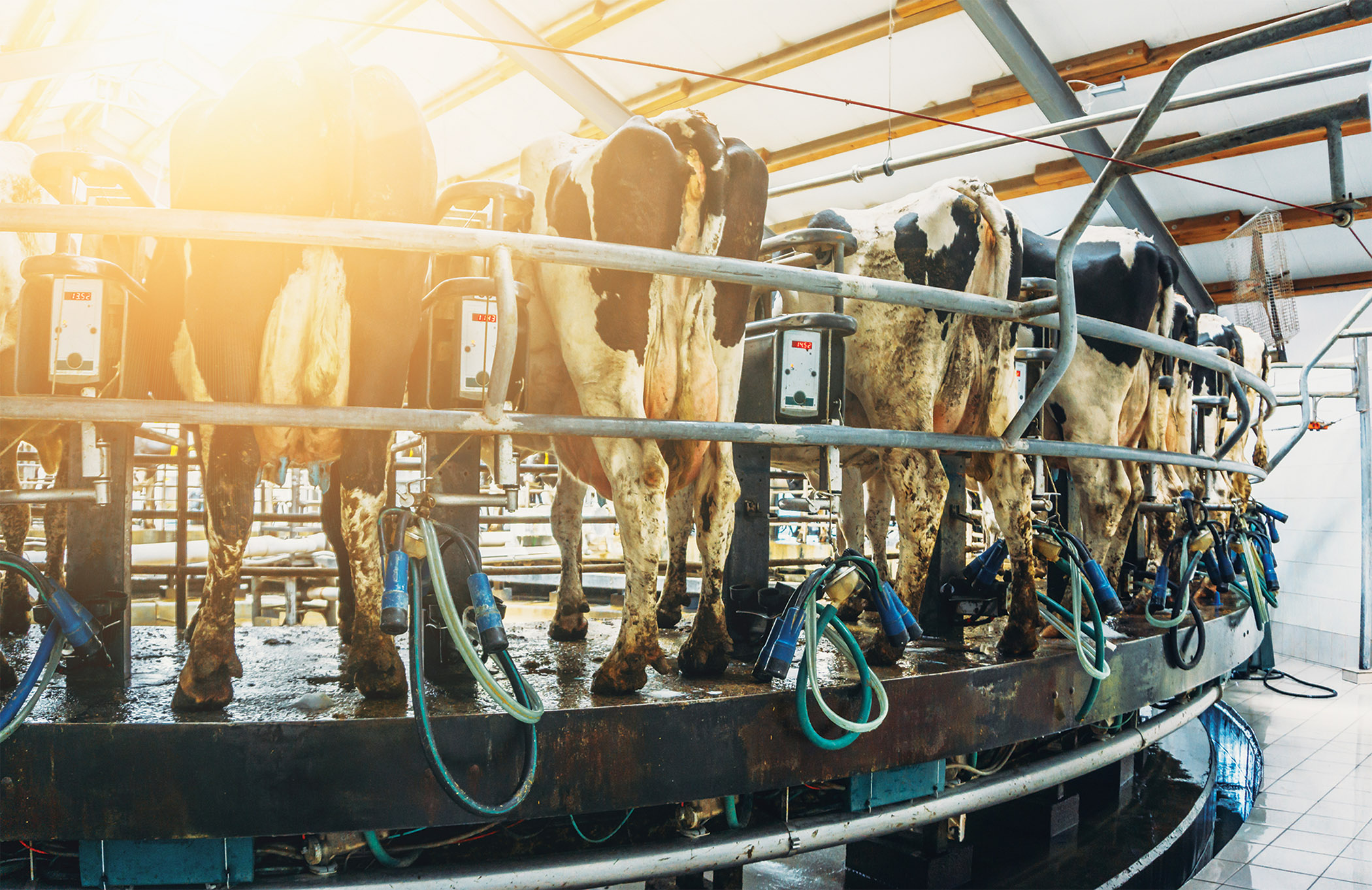
Today’s Parlor Designs
By Maura Keller
Ben Streitmatter, regional sales manager at FBi Buildings, says the key factors influencing the choice of parlor system include existing facilities, labor availability, and budget. Priorities such as cow comfort, labor efficiency, and milk quality are also central facets of parlor design for dairy producers.
As he explains, robotic systems offer high automation and reduced labor, while rotary, parallel, tandem, and swing-over parlors provide flexible, cost-effective alternatives tailored to specific operational needs.
“One major advancement to note is recent strides in construction capabilities. With progress in innovative design, efficient engineering review, and highly competent construction crews, the amount of time it takes to remodel or construct new dairy facilities has been greatly reduced,” Streitmatter says. “This shift in timeliness reduces the overall cost of construction in many cases and allows the producer more flexibility with the integration of new facilities into their operation.”
At FBi Buildings, they specialize in constructing a variety of facilities for the dairy industry, including parlors, freestall barns, commodity storage facilities, digester buildings, and more.. By leveraging strategic industry partners for design, installation of milking systems, cow comfort enhancements, sustainability features, and more, they ensure that they provide fully functional, state-of-the-art dairy facilities tailored to each client’s specific needs.
Andrew Hughes, sales specialist – dairy equipment at GEA Farm Technologies, points out that rotary parlors are largely the design of choice for many of today’s dairy operations and in parallel parlor designs the advancement of the vertical lift parlor stall has become the most popular design.
GEA has redesigned and branded its rotary parlor product line to be the T8000 line with two models – the T8850 and T8900.
“Our vertical lift parlor line includes our Magnum and Global Low Profile Vertical lift parlor stalls,” Hughes says.
According to Amy Steinke, director, product management and marketing at BouMatic, she’s also seeing some advancements that the dairy industry is seeing today in regard to parlor design.
“The industry is looking for more data and knowledge not only about milk yield, but data related to the milk components such as fat, protein, and lactose,” Steinke said. “Herd health can be monitored by the ratio of fat and protein in the milk. Health factors like milk fat depression (MFD) and negative energy balance (NEB) can be detected and treated.”
Most recently, BouMatic is combining efforts with Brolis Sensor Technology on integrating the Brolis in-line milk analyzer from the Brolis HerdLine concept. The in-line milk analyzer continuously monitors fat, protein, and lactose. This data will help dairy farmers to improve milk quality, detect early stages of disease and make decisions on genetic selection and feeding strategy.
“The Brolis HerdLine delivers greater control and oversight over the dairy herd,” said Steve Pretz, president of BouMatic. “Efficiency and sustainability of dairy farms depends on data needed to make key decisions.”
As Pretz further explained, this milk analyzer is the first of several innovations that BouMatic intends to bring to the market soon as part of the ‘cow side’ technology movement. “These devices are critical to the development of precision farming but will also be a key element in developing cutting edge tools for the world’s largest farms,” he said. “We will provide a unique value proposition to farms of all sizes.”
To streamline costs, Austin Turner at Turner Inc. is also seeing a trend for the last five or six years of dairy producers remodeling and upgrading their existing parlor designs.
“Right now, new parlors only account for about 25% of what we sell,” Turner says. “The rest are retrofits and upgrades of existing parlor equipment. We work with producers to retrofit their individual space.” Turner’s bolt-together design options allow for perfect customization for each parlor’s needs and the Turner Standard Parallel Stall is the company’s original design and is a favorite among many daily producers.
Considerations To Make
When it comes to parlor design components, Hughes says the “top of the list” for all designs is cow-friendly designs as well as operator efficiency.
“I believe the additional ‘must haves’ are structural designs for longevity, stainless steel for corrosive resistance as well as designs for component longevity. This is especially important with farms using sand bedding,” Hughes says. “Some of the new hygiene products being introduced in place of the traditional iodine can have a corrosive effect on parlor components while being very effective for killing bacteria and disinfecting teats.”
Streitmatter stresses that producers looking to design or upgrade dairy parlor facilities should prioritize key components to maximize efficiency, cow comfort, and milk quality. Essential features include soft flooring, gentle handling systems, effective cleaning mechanisms, and efficient milking automation.
“Ensuring proper ventilation, ergonomic layouts, and integrated data monitoring enhances operational effectiveness. Sustainability measures such as energy efficiency and water management are also crucial,” Streitmatter says. “Additionally, investing in a quality building structure ensures durability and longevity, safeguarding the farm’s investment over time. By integrating these ‘must haves,’ dairy farms can optimize productivity, promote cow welfare, and adhere to regulatory standards while preparing for future advancements in dairy technology.
Steinke adds that dairy producers also recognize that the top “must haves” include some sort of identification, whether it is a per-point identification system or an activity neck tag.
She pointed out that ear tags have a relatively low performance due to their need to “compete” with environmental electrical noise which deteriorates their ID performance.
“Being able to properly identify the animal allows for the data being gathered to link to a specific animal,” Steinke said.
There are also key mistakes producers should avoid as it relates to parlor design. From Steinke’s experience, cow flow is an area that sometimes gets overlooked. As she explained, by not allowing enough room for entrance and exits regardless of parlor style, it can put undue stress on the animal and slow down the parlor throughput and can also cause the ID system to be less effective.
One area Hughes believes that many producers overlook is overall space. Utility rooms can fill up fast with the vacuum pumps, air compressors, hot water prep equipment, water systems and hygiene products.
“As we move into more on farm blending of hygiene products versus the ready-to-use traditional products, this comes with more space for the additional equipment,” Hughes says. “Two things I believe are important are employee space including bathrooms close to the work area, which can make it easier for employees and also more efficient to monitor employee movement. Secondly, I think parlor ventilation can be overlooked. This is important for employees and animals but also for equipment longevity.”
Equipment that is clean and dry leads to longer life as well as better operating performance overall.
“Often overlooked in dairy facility design are essential aspects such as efficient layouts, cow comfort, and the integration of modern milking technologies,” Streitmatter says. “Sustainability considerations and the choice of high-quality materials are also frequently neglected. In my experience, expert design and construction services play a pivotal role in addressing these challenges. They ensure that dairy facilities are optimized for efficiency, prioritize cow welfare, and integrate advanced technologies, all while implementing sustainable practices. This holistic approach not only boosts operational productivity and profitability but also fosters long-term sustainability within the operation.”
Hughes also notes that overall designs may not take into consideration how much the operation may grow in the future. “I have seen too many times that just a few years into a new milking center, space runs out very quickly as the operation grows or new technology is adapted,” he says.
Steinke agrees. “Another thing producers need to keep in mind are any future plans,” Steinke said. “If they do have plans to expand their herd, they may want to try to accommodate for those future expansions. This entails looking at vacuum and cooling sizing as well as the actual building layout.”
Designs for a parlor need to ensure the overall real estate allows for future expansion for technologies. Items like automated teat dip and sprayers and herd management systems could take up a footprint that was not accounted for when first outlining the parlor.
Down the Road
Like most technologies and production systems within the dairy industry, parlor design faces continuous advancements in the overall technology involved.
“Producers have options as to which technology they wish to pursue. Some prefer the flexibility and lower labor usage that milking robots bring,” Steinke said. “Rotaries are known for milking a high number of cows and will allow for herd expansion easier and also allows for labor efficiencies. The milking robot will ‘call’ a farmer when it needs attention and that works for some. Other farmers prefer to maintain the schedule that a rotary can provide. Farms have different goals, objectives, and performances they wish to achieve. They will make their parlor style decisions based on those goals.”
Hughes points out that new technology in milk evaluation, new metering technology that can incorporate components evaluation, cow side milk testing for pregnancy, and measuring Somatic cell and mastitis presence are all on the horizon.
In addition, rotary parlors are evolving quickly to add robotic teat prep, and pre- and post-teat dip application.
“These new devices are positioned to make overall efficiency of the system better while looking at the overall labor needs and requirements for the operation,” Hughes says. “Labor is a large concern for operations of all sizes. New technology will be introduced into the market very soon from GEA automating the teat prep and milking process for a single attachment that automates all of these processes into one single step. The future designs of parlors will be looking at how to do the most with the least.”
Streitmatter believes future dairy facility designs will continue to advance with a strong emphasis on efficiency, data analytics, and infrastructure longevity. He expects these designs will feature modular and flexible layouts to cater to varying herd sizes and management preferences. Renewable energy sources like solar, wind, and biogas will increasingly be integrated to reduce costs and environmental impact.
“Emphasizing enhanced cow comfort through improved flooring, ventilation, and ergonomic designs will also be pivotal,” Streitmatter says. “These innovations, alongside innovative building practices, aim to optimize productivity, sustainability, and animal welfare in dairy operations, aligning with evolving industry trends and consumer expectations for responsibly sourced dairy products.”